Topic of the week: GB Railfreight Unveils Revolutionary Class 99 Locomotives
GB Railfreight (GBRf) has unveiled its new Class 99 locomotives at its Peterborough headquarters, marking a major leap forward for sustainable transport in the UK. The £150 million investment represents a significant commitment to reducing carbon emissions and supporting regional growth.
The Class 99 locomotives are designed to run on both electricity and renewable fuels, offering customers the most sustainable freight solution on the market and halving carbon emissions. This hybrid power system allows the locomotives to operate on electric lines where available and switch seamlessly to renewable fuels elsewhere, ensuring that goods arrive at their destination sooner and more reliably.
The new fleet will support critical projects and stock shops nationwide, transporting a vast range of consumable goods and materials across the country. The Class 99s will play a key role in decarbonising Britain's rail freight network, reducing emissions by more than half on a typical journey.
The introduction of the Class 99 locomotives is expected to have a significant impact on the rail freight market, driving growth and reducing emissions. The new fleet will support regional growth, easing pressure on the nation's transport infrastructure, and contributing to the UK economy. The Class 99s will set a new standard for green rail freight, supporting customers to meet their sustainability targets and lead the race to zero emissions.
Once testing is complete, the new locomotives will enter commercial service this winter.
Sea:
- Over the last two weeks China/East Asia to North America West Coast spot rates have decreased by 30.1% from $3,388/FEU to $2,368/FEU according to Freightos data.
- China/East Asia to North America East Coast spot rates have fallen over the last two weeks, decreasing by 20% to $4,888/FEU.
- Global container spot prices have fallen over the last two weeks, and are now sitting at $2,541/FEU, a 12.2% decrease over the last two weeks and a 49.7% decrease from spot rates this time in 2024 according to the Freightos Baltic Index (FBX)
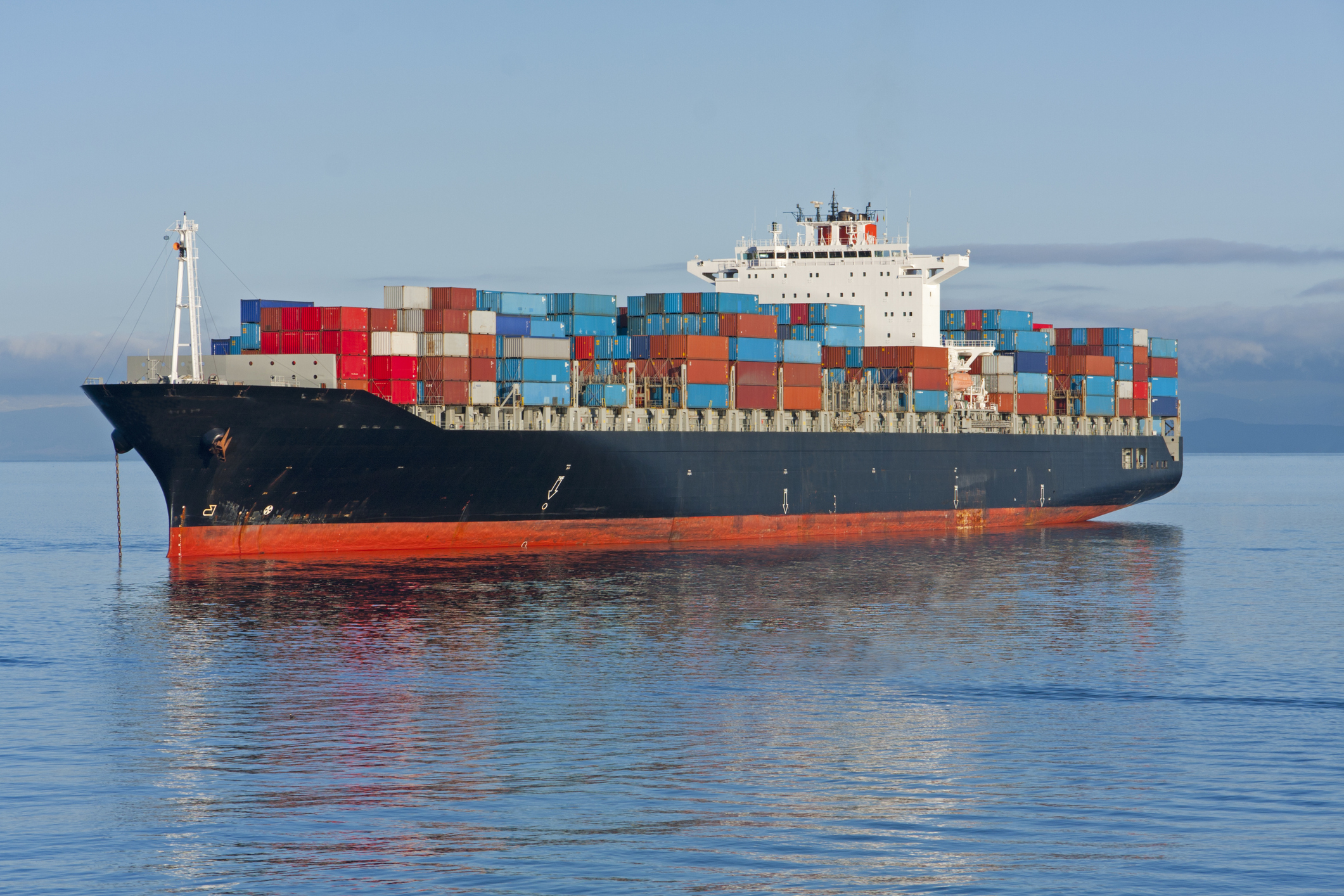
Air:
- Global Air Freight spot rates currently sit at $2.29, as rates continue to fluctuate according to the Freightos Air Freight Index (FAX)
- Europe to Northern America spot rates currently sit at $1.79 (100-3000kg), says FAX, remaining unchanged.
- Europe to Asia, Greater China spot rates currently sit at $1.15 (100-3000kg), says FAX, decreasing by 1.7%.
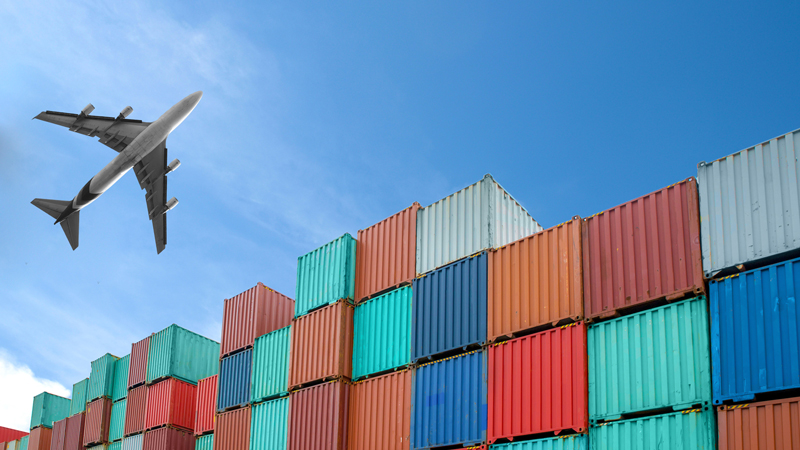
That’s all for this week’s update…
Check out our other insights and articles for more in depth industry news and trending topics, or get in contact to discuss some of our best in class freight forwarding services!